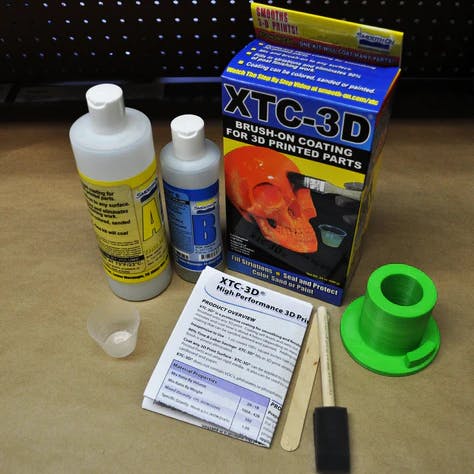
XTC-3D Coating: High-Performance 3D Printing Guide
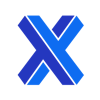
XTC-3D™ is a specialized coating designed to enhance the finish of 3D-printed objects. This two-component system effectively smooths out the print lines, providing a high-gloss, protective layer without degrading the plastic. It involves a straightforward application process: mixing the resin and hardener in a 2:1 ratio, applying the mixture to the print, and allowing it to cure. Proper use requires basic safety precautions and can be followed by sanding for an even smoother finish. XTC-3D offers an excellent solution for improving the aesthetic and structural integrity of 3D printed parts.
This article will discuss what XTC-3D is, how it is used, its application, and its compatibility with different 3D printing filaments.
What Is XTC-3D?
XTC-3D is a high-performance 3D print coating product produced by Smooth-On, Inc. It's essentially an epoxy resin designed specifically for coating and finishing 3D-printed parts. It can be applied to most 3D-printing materials, including: PLA, ABS, HIPS, PETG, nylon, powder printed parts, using a brush. The product gives a smooth glossy finish and will not affect the color of the printed part.
When applied, XTC-3D self-levels and cures to a hard, impact-resistant finish that can be sanded, primed, and painted. The product is mixed in a 2:1 ratio by volume and has a relatively low odor compared to other resins. Its thin viscosity allows it to cover 3D printed objects without obscuring fine details, and it can be used to prepare models for painting, metal plating, or for use as a finished product. The coating also enhances the strength of 3D-printed parts, making them more durable for practical use. The application, or working time, is about 10 minutes with a cure time of roughly 4 hours.
What Is the Use of XTC-3D?
The XTC-3D coating compound offers multiple benefits to enhance the appearance, durability, and usability of prints. Here’s a deeper look into its uses:
1. Surface Smoothing
One of the primary uses of XTC-3D is to smooth the surface of 3D-printed parts. 3D printing often leaves layer lines or printing marks that can detract from the appearance and feel of the object. Applying XTC-3D fills in these gaps and irregularities, resulting in a much smoother surface. This is particularly beneficial for models that require a high level of detail or a sleek, aesthetic finish.
2. High Gloss Finish
Beyond just smoothing, XTC-3D can be used to achieve a high-gloss finish on 3D-printed objects. When applied correctly, it leaves a shiny, reflective surface that enhances the visual appeal of the print. This glossy finish can be further polished or left as is, depending on the desired outcome. It's ideal for display models, prototypes, and any print that benefits from a shiny appearance.
3. Durability Enhancement
3D-printed parts can sometimes be fragile, depending on the material and the structure of the object. XTC-3D adds a layer of protection that enhances the durability and strength of the prints. This makes them more suitable for functional use whenever wear and tear might otherwise quickly degrade an untreated print. The epoxy resin forms a hard, impact-resistant surface that protects the underlying material from scratches, dents, and breaks.
4. Versatile Application
XTC-3D is designed to work with a wide range of 3D printing materials, including: PLA, ABS, and PETG. Additionally, it can be applied as a coating for wood, plaster, fabric, cardboard and paper, as well as EPS, EPDM, and urethane foam. This versatility means it can be used for a broad spectrum of projects, from hobbyist models to professional prototypes. Whether the object is intended for decorative purposes or practical application, XTC-3D can enhance its qualities without compromising the material's integrity.
5. Ease of Use
Despite its professional-grade results, XTC-3D is formulated to be user-friendly. It mixes in a simple 2:1 ratio and can be applied with relative ease, leveling itself out over the surface of the print. This self-leveling property minimizes the need for extensive post-application finishing, making it accessible for users of all skill levels. The low odor and simple cleanup further contribute to its ease of use.
Can XTC-3D Be Used in 3D Smoothing?
Yes, XTC-3D can be used for 3D smoothing. It's one of its primary uses. XTC-3D, being an epoxy-resin coating, is designed specifically to smooth out the layer lines and surface imperfections commonly found on 3D-printed parts. When applied to a 3D-printed object, it fills in the gaps between the print layers, creating a smooth, level surface.
To achieve the smoothing effect, the mixed XTC-3D resin is applied over the 3D-printed part. It has a low viscosity, which allows it to flow and self-level, covering the surface intricacies without obscuring details. Once cured, the treated surface can be further sanded if necessary, but in many cases, the self-leveling property of XTC-3D reduces or eliminates the need for extensive post-processing.
How To Use XTC-3D?
Here are the general steps on how to use XTC-3D:
- Safety First: Wear gloves and work in a well-ventilated area. XTC-3D can produce harmful fumes if inhaled in large quantities, and it can irritate the skin on contact.
- Prepare Your Work Area: Cover your work surface with wax paper, plastic sheeting, or any other protective covering to prevent sticking. Have mixing and application tools ready, such as: mixing cups, stir sticks, and brushes or foam applicators.
- Measure the Components: XTC-3D is a two-part system consisting of a resin (Part A) and a hardener (Part B). The mix ratio is typically 2 parts A to 1 part B by volume. Accurately measure the amounts needed for your project using a mixing cup.
- Mix the Components: Pour Part A and Part B into a mixing cup and stir thoroughly for at least one minute, ensuring that you scrape the sides and bottom of the mixing cup to fully blend the components. Avoid introducing air bubbles while mixing.
- Apply to the 3D Print: Once mixed, apply the XTC-3D to your 3D-printed part using a brush or foam applicator. Work quickly, as you'll have a limited working time of about 10 minutes before the mixture begins to thicken and cure. Aim for a thin, even coat to avoid drips or pooling. For best results, apply in one direction to minimize brush marks.
- Curing: Allow the coated object to cure at room temperature. Curing time can vary depending on the ambient temperature and humidity, but it's typically around 4 hours for it to become tack-free. For a full cure, it is often recommended to wait 24 hours.
- Sanding and Finishing: After the XTC-3D has fully cured, you can sand the surface to remove any imperfections or brush strokes and to achieve an even smoother finish. Start with a coarse grit sandpaper and work your way up to a fine grit for a polished surface. If necessary, additional coats of XTC-3D can be applied for thicker coverage, repeating the mixing, applying, curing, and sanding processes.
- Painting (Optional): If desired, the finished and cured object can be painted. Ensure the surface is clean and free of dust before applying paint.
What Are the Considerations When Using XTC-3D?
When using XTC-3D for 3D-printed objects, there are several important considerations to keep in mind to ensure optimal results and safe use. Here are the key factors:
- Protective Gear: Always wear gloves and safety glasses to protect your skin and eyes from the epoxy resin and hardener. A mask may also be necessary if you're sensitive to fumes or working in a poorly ventilated area.
- Ventilation: Work in a well-ventilated space to minimize inhalation of any potentially harmful vapors.
- Cleanliness: The 3D-printed part should be clean and free of any oils, dust, or debris to ensure good adhesion of the XTC-3D.
- Accurate Mixing: It's crucial to mix the resin (Part A) and hardener (Part B) at the correct 2:1 ratio by volume. Inaccurate mixing can lead to a tacky finish or incomplete curing.
- Thorough Mixing: Ensure the mixture is stirred thoroughly for at least one minute, scraping the sides and bottom of the mixing container to avoid any uncured spots.
- Application Thickness: Apply XTC-3D in thin, even coats to prevent running or pooling, which can obscure details of the print.
- Pot Life: Be aware of the pot life (approximately 10 minutes at room temperature) and work quickly to apply the mixture before it begins to thicken and cure.
- Curing Time: Allow the coated object to cure for at least 4 hours at room temperature, with a full cure and maximum hardness achieved in 24 hours.
- Temperature and Humidity: The curing time can vary based on ambient temperature and humidity. Higher temperatures can accelerate curing, while high humidity can affect the finish.
- Sanding: If sanding is required for further smoothing, wait until the XTC-3D is fully cured. Use progressive grits for the best finish.
- Painting: Ensure the XTC-3D is fully cured before painting. The smooth surface adheres well to most types of paint.
- Immediate Cleanup: Clean your tools and mixing containers with acetone or isopropyl alcohol immediately after use, before the mixture hardens.
- Test First: If possible, conduct a small test on a similar material or inconspicuous area to ensure compatibility and understand the working properties of XTC-3D.
What Are the Benefits of Using XTC-3D?
There are several benefits of using XTC-3D such as:
- Fills in the print lines in 3D-printed objects, providing a smooth, glossy finish.
- The coating is mixed in a 2:1 ratio and can be applied with a brush. It's self-leveling, meaning it will spread out evenly over the surface of the print.
- Can increase a product's strength and durability. The coating adds a protective layer that can help resist impacts and wear over time.
- Once the XTC-3D has cured, the surface can be sanded and painted. This allows for a high degree of customization and finishing options.
- Is compatible with a wide range of 3D-printing materials, including: PLA, ABS, Nylon, and PETG.
- Instead of needing to use expensive or complex post-processing techniques to achieve a smooth finish, XTC-3D offers a relatively inexpensive solution.
Is There Any Risk in Using XTC-3D?
Using XTC-3D, like working with any chemical product, does come with its set of risks and precautions that should be adhered to for safe use. Here are some of the risks and considerations:
- Chemical Exposure: XTC-3D is a chemical epoxy, and exposure can irritate the skin, eyes, and respiratory system. Direct contact with the skin can lead to allergic reactions in some individuals. It's important to use protective gloves, eye protection, and, in some cases, a respirator to avoid irritation or allergic reactions.
- Ventilation: Proper ventilation is crucial when working with XTC-3D because the fumes can be harmful if inhaled in concentrated amounts. Working in a well-ventilated area or using a fume extractor can help minimize exposure to these fumes.
- Combustibility: While not highly flammable, like all resins, XTC-3D should be kept away from open flames and heat sources to prevent any risk of combustion.
- Proper Mixing and Curing: Incorrect mixing ratios or incomplete mixing can lead to issues with curing, resulting in a tacky or soft finish. This not only affects the aesthetic and functional quality of the finished piece but can also create a situation in which uncured resin remains, which could be more chemically reactive and potentially harmful.
- Disposal: Disposal of XTC-3D and any related waste (such as mixed but unused product, containers, and applicators) needs to be done carefully to avoid environmental harm. Following local regulations for the disposal of chemical products is important.
Does XTC-3D Suitable for Filament-Based 3D Printing?
Yes, XTC-3D is very suitable for filament-based 3D printing. It is specifically designed to be used with common 3D printing filaments such as PLA and ABS. It is used to improve the finish of printed objects made from these materials. By applying a thin coat of XTC-3D, users can effectively smooth out the layer lines that are characteristic of filament-based 3D prints, resulting in a much smoother and more professional-looking surface.
What Are the Different Filament-based 3D Printing That Is Suitable for XTC-3D?
XTC-3D is compatible with a wide range of filament-based 3D printing materials. Here's how it works with the specific filaments listed:
1. PLA
PLA is one of the most popular 3D printing materials due to its ease of use, biodegradability, and low warping tendency. XTC-3D can be applied to PLA prints to smooth out layer lines and imperfections, providing a glossy or matte finish based on how it's sanded and painted afterward. It enhances the visual appeal and structural integrity of PLA objects without compromising their details.
2. ABS
ABS is known for its toughness and heat resistance, making it ideal for functional parts. However, its surface can often be rough or have visible layer lines. XTC-3D effectively smooths these surfaces, offering an improved aesthetic and smoother feel. It also helps in sealing the surface, making ABS parts more resistant to moisture and chemicals.
3. PETG
PETG combines the ease of printing achieved with PLA with the strength and durability of ABS. XTC-3D is excellent for PETG prints, smoothing out layers and adding a protective coat that enhances its natural properties like clarity and color vibrancy, besides increasing its resistance to impact and temperature variations.
4. ASA
ASA is similar to ABS but with added UV resistance, making it perfect for outdoor use. Applying XTC-3D to ASA prints not only smooths and beautifies the surface but also adds an extra layer of protection against weathering, further extending the life span of outdoor parts.
5. TPU
TPU is a flexible, rubber-like material. While XTC-3D is generally used on rigid materials, it can also be applied to TPU prints to smooth surfaces without significantly affecting their flexibility. This application is ideal for creating smoother, more aesthetically pleasing flexible parts, though the amount applied must be controlled to maintain flexibility.
6. Nylon
Nylon is prized for its strength, flexibility, and durability, making it suitable for functional parts that require resistance to wear and impact. XTC-3D can be used on nylon prints to enhance their appearance by reducing layer visibility, and to seal the surface, which helps in preventing moisture absorption—a common issue with nylon materials.
What Are Alternatives to XTC-3D?
Alternatives to XTC-3D for improving the finish of 3D-printed parts span a range of products and techniques, each with its advantages and applications. Here are several alternatives that are commonly used in the 3D printing community:
- Sanding and Priming: Sanding the print manually with sandpaper of various grits can significantly smooth the surface. Following up with a primer (especially one designed for 3D prints) can further smooth the surface and prepare it for painting.
- Acetone Vapor Smoothing: Specifically for ABS prints, acetone vapor smoothing involves exposing the print to acetone vapors in a controlled environment. The acetone slightly melts the surface, smoothing out layer lines. This method is highly effective but requires careful handling due to acetone's flammability and toxicity.
- Epoxy Resins: General-purpose epoxy resins can be used similarly to XTC-3D to coat and smooth 3D-printed parts. Epoxy resins are available in various formulations, some of which are more viscous and suitable for filling in larger gaps and imperfections.
- PolySmooth™ and Polishing Machine: Polymaker offers a filament called PolySmooth™, designed to be easily smoothed with their Polysher™ device, which uses isopropyl alcohol mist to smooth the print.
- Polyurethane Coating: Polyurethane coatings can offer a durable, smooth finish while also providing additional properties like UV resistance and flexibility, depending on the formulation. These coatings are available in both spray and brush-on applications.
- Polishing Compounds: For materials like PLA and PETG, which cannot be smoothed with acetone, mechanical polishing with a polishing compound can be an effective way to achieve a glossy finish. This method requires a lot of manual labor and care to avoid overheating and melting the plastic.
- Dichloromethane (DCM) Smoothing: Similar to acetone vapor smoothing but applicable to a wider range of plastics, including PLA, DCM smoothing involves exposing the print to dichloromethane vapors. It's effective but must be handled with extreme care due to its potent health risks and environmental impact.
- Heat Gun: Using a heat gun can smooth the surface of certain types of 3D-printed plastics. The heat slightly melts the outer layer, reducing the appearance of layer lines. This method requires precision to avoid warping or excessive melting of the part.
- Cold Welding: For minor imperfections, cold-welding compounds (special adhesives that can chemically bond plastic parts at room temperature) can fill in gaps and seams. After curing, the excess can be sanded down for a smooth finish.
- Chemical Smoothing for PLA With Ethyl Acetate: Smoothing PLA chemically is challenging and hazardous. Ethyl acetate is an effective but risky choice due to its high flammability and toxicity. It’s also difficult to obtain. For PLA, a safer and more accessible option would be using PVB (polyvinyl butyral)-based solutions, designed for easier and safer smoothing.
Is XTC-3D a Type of 3D Coating?
Yes, XTC-3D is a type of 3D coating specifically formulated to enhance and finish 3D-printed objects. It is an epoxy-resin-based coating that is designed to be applied over the surface of 3D prints to smooth out layer lines, fill in gaps, and provide a more uniform and aesthetically pleasing finish. Once applied, it cures to a hard, clear finish that can be sanded, painted, or machined, making it versatile for various post-processing needs.
Summary
This article presented XTC-3D high performance 3D print coating, explained it, and discussed how to use it and its various benefits. To learn more about 3D print coats, contact a Xometry representative.
Xometry provides a wide range of manufacturing capabilities, including 3D printing and other value-added services for all of your prototyping and production needs. Visit our website to learn more or to request a free, no-obligation quote.
Copyright and Trademark Notices
- XTC-3DTM is a trademark of Smooth-On, Inc., Macungie, PA 18062
- PolySmoothTM and Polysher™ are trademarks of Polymaker
Disclaimer
The content appearing on this webpage is for informational purposes only. Xometry makes no representation or warranty of any kind, be it expressed or implied, as to the accuracy, completeness, or validity of the information. Any performance parameters, geometric tolerances, specific design features, quality and types of materials, or processes should not be inferred to represent what will be delivered by third-party suppliers or manufacturers through Xometry’s network. Buyers seeking quotes for parts are responsible for defining the specific requirements for those parts. Please refer to our terms and conditions for more information.
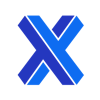