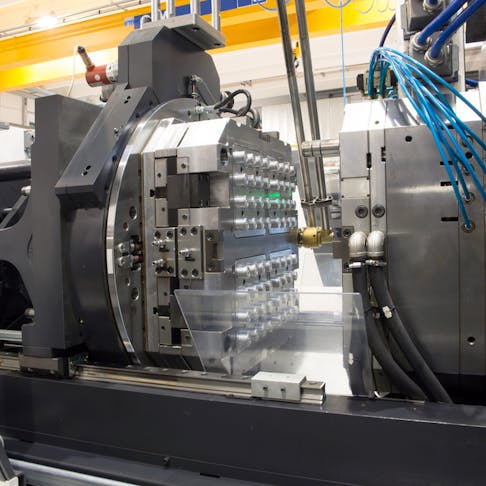
Gas Assist Injection Molding: Definition, Purpose, and Process
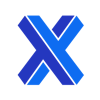
Gas assist injection molding is an innovative technique used in the manufacturing industry to produce high-quality plastic components with hollow sections or complex geometries. This process involves injecting a pressurized gas, typically nitrogen, into the mold cavity after the initial plastic injection, displacing some of the molten plastic and forming hollow areas within the final product.
Gas assist injection molding reduces material costs, cycle times, and part weight by using gas instead of additional plastic material. It also increases the design flexibility of the finished product and its overall structural integrity. Numerous industries, including those that demand lightweight, complex components, such as automotive, consumer goods, and electronics, find extensive use for this technique. This article will discuss the benefits and applications of gas-assist injection molding, as well as its function and method.
What Is Gas Assist Injection Molding?
Gas assist injection molding (GAIM) involves injecting plastic material into mold cavities. However, only about 70% to 80% of the mold volume is filled with plastic when using gas assist injection molding. The plastic material is displaced by the use of high-pressure gas, such as nitrogen, within the thicker areas of the part, creating hollow sections. This method makes it possible to produce plastic parts that are lightweight, intricate, and structurally sound.
Who Invented Gas Assist Injection Molding?
Gas assist injection molding was invented by James Watson Hendry, an American inventor, in the 1970s. This ground-breaking method allowed for the rapid cooling of complex, hollow objects. It improved design flexibility, increased part strength and surface finish, decreased production time, cost, weight, and waste, and revolutionized the manufacturing sector. Although the idea was first proposed in the 1970s, gas assist injection molding didn't gain widespread commercial acceptance until the 1990s.
To learn more, see our guide on Injection Molded Plastic.
What Is the Primary Purpose of Gas Assist Injection Molding?
The primary purpose of gas assist injection molding is to improve the quality and efficiency of plastic part production. It involves injecting pressurized gas into the molten plastic during the molding process. This technique helps reduce material usage, minimize sink marks, eliminate warpage, and enhance surface finish. Gas assist injection molding is particularly useful for large, thick-walled parts or parts with complex geometries.
What Is the Importance of Gas Assist Injection Molding?
Gas assist injection molding holds significant importance in the manufacturing process due to several reasons. Firstly, it allows the production of high-quality parts with complex geometries, without compromising their appearance or functional performance. Secondly, it offers material savings by requiring less plastic material compared to conventional injection molding methods. Lastly, it enables the reduction of part weight, often achieving weight reductions of up to 40%, resulting in cost savings and improved production efficiency.
How Does Gas Assist Injection Molding Work?
Gas assist injection molding involves a three-stage process. First, a plastic resin is injected into the mold cavity, but only to a degree that partially fills it (due to the intention for the final part to include hollow sections). Second, pressurized gas, often nitrogen, is introduced, creating a bubble inside the resin. This gas expands, exerting pressure and pushing the molten resin against the surfaces of the mold. In the third stage, a secondary gas penetration phase occurs to compensate for thermal contraction. Additional gas flows into the mold to fill gaps, maintaining uniform pressure and preventing deformations. This process ensures efficient filling of the mold, reduces material usage, and produces high-quality, structurally sound parts. After the plastic has solidified, the gas is released, and the parts are extracted from the mold.
How Does Gas Assist Injection Molding Differ From Injection Molding?
Gas assist injection molding differs from conventional injection molding in several ways. In gas-assist molding, the pressure applied is lower because there is less material to pack into the mold, primarily due to the presence of hollow sections in the part design. On the other hand, the pressure applied in injection molding is higher because the mold cavity needs to be completely filled with molten material to create solid parts. High pressure is necessary to ensure that the material flows into all the intricate details and corners of the mold.
Additionally, the pressure in gas assist molding is generated by gas rather than the thick, viscous liquid of conventional injection molding. This results in lower frictional losses within the pressurized medium, as the gas has a lower viscosity compared to molten plastic used in traditional injection molding processes.
What Is the Gas Assist Injection Molding Process?
The gas assist injection molding process involves injecting plastic resin into a mold cavity, followed by the introduction of pressurized gas, typically nitrogen. The gas forms a bubble inside the resin, exerting pressure to fill the mold. After curing, the nitrogen is vented, and the gas assist injection molded parts are removed.
What Is the Gas Used in Gas Assisted Injection Molding?
The gas commonly used in gas-assisted injection molding is nitrogen. Nitrogen is preferred due to its inert nature and availability. It is non-reactive with most plastics and does not affect the properties or appearance of the molded parts. Nitrogen is introduced into the mold cavity under pressure to assist in the filling and packing stages, ensuring proper material distribution and reducing the use of plastic resin.
What Are the Materials Used in Gas Assist Injection Molding?
Materials commonly used in gas assist injection molding include:
1. Polypropylene (PP)
Polypropylene is a thermoplastic material that is widely used in gas assist injection molding due to its favorable properties. It exhibits good chemical resistance, making it suitable for applications involving contact with various substances. Additionally, PP has low electrical conductivity, making it useful in electrical and electronic components. Its toughness and high melting point contribute to its strength and ability to withstand mechanical stresses. Polypropylene's heat resistance and ability to maintain dimensional stability make it a reliable choice for gas assist injection molding. However, one potential drawback of PP is its susceptibility to UV degradation, which can limit its outdoor applications.
To learn more, see our guide on What is PP Material.
2. Polycarbonate (PC)
Polycarbonate is a popular material in gas assist injection molding due to its exceptional impact resistance. It can withstand high-impact forces, making it suitable for applications in which strength and durability are crucial, such as automotive components and safety equipment. Polycarbonate also exhibits high resistance to wear and abrasion, extending the life span of the molded parts. Another advantage is its ability to maintain toughness and mechanical properties over a wide temperature range. However, polycarbonate can be relatively expensive compared to other materials, which may affect its cost-effectiveness in certain applications.
For more information, see our guide on All About Polycarbonate.
3. Acrylonitrile Butadiene Styrene (ABS)
ABS is a versatile and widely used material in various plastic manufacturing processes, including gas assist injection molding. It offers a combination of strength, durability, and lightweight characteristics, making it suitable for a range of applications. ABS is impact-resistant, allowing it to withstand sudden forces without breaking, which is particularly beneficial in automotive components, protective casings, and consumer goods. However, ABS can be prone to warping and may require careful control of processing parameters to prevent dimensional inaccuracies in complex parts.
4. High-Density Polyethylene (HDPE)
HDPE is a popular choice for gas assist injection molding due to its desirable properties. It exhibits excellent weather resistance, making it suitable for outdoor applications in which exposure to UV radiation and harsh environmental conditions is expected. HDPE is also chemically resistant, enabling it to withstand exposure to a wide range of chemicals without degradation. Additionally, HDPE is known for its strength and toughness, maintaining its mechanical properties even in extreme temperatures. However, HDPE may exhibit lower stiffness compared to other materials, which can affect dimensional stability in certain applications.
For more information, see our guide on HDPE Properties.
5. High Impact Polystyrene (HIPS)
High Impact Polystyrene is chosen for gas-assist injection molding when impact resistance is a critical requirement. HIPS possesses good impact strength and dimensional stability, making it suitable for packaging materials, consumer goods, and other applications that may experience rough handling or potential impacts. It is relatively easy to process, providing manufacturers with cost-effective and efficient production capabilities. However, HIPS may not offer the same level of chemical resistance as other materials. This limits its suitability for certain environments or applications that involve exposure to aggressive chemicals.
What Are the Applications of Gas Assist Injection Molding?
Gas assist injection molding has various applications, including:
- Automotive: Lightweight instrument panels, door panels, and seat backs.
- Consumer Products: Furniture components such as chair backs, appliance parts, and toys.
- Aerospace: Air ducts, seat frames, interior panels.
- Electronics: Enclosures, housings, structural components.
- Industrial Equipment: Handles, enclosures, structural parts.
What Are Examples of Gas Assist Injection Molding Products?
Gas assist injection molding products are characterized by hollow sections or voids created within the molded part using high-pressure gas. Some examples of products that can be manufactured using gas assist injection molding include:
- Door panels
- Instrument panels
- Armrests
- Bicycle frames
- Golf club heads
- Electronic enclosures
- Motorcycle helmets
- Tool handles and grips
- Storage containers
Are Gas Assist Injection Molding Products Durable?
Yes, gas assist injection molding products can be durable. The process allows for the creation of lightweight parts that are still firm. The hollow sections created by gas assist provide strength and durability while reducing overall weight. Additionally, these products can withstand impact forces, making them suitable for applications in which durability is required.
How Long Do Gas Assist Injection Molding Products Last?
The life span of gas assist injection molding products depends on a variety of factors, including the material used, the design, and part usage. However, when properly maintained and used under normal conditions, these products can last for many years. The durability and longevity of gas assist injection molding products depend on factors specific to each application and product.
What Are the Advantages of Gas Assist Injection Molding?
Advantages of gas assist injection molding include:
- Enhanced control over part dimensions and tolerances.
- Faster cycle times and increased productivity.
- Reduced surface imperfections, resulting in a high-quality finish.
- Decreased warpage, sink marks, and internal stresses.
- Lower material costs due to hollow sections.
- Achieves strength and rigidity with reduced weight.
What Are the Disadvantages of Gas Assist Injection Molding?
Disadvantages of gas assist injection molding include:
- Difficulty with multiple cavities of different sizes. The entire mold is needed to be removed if one cavity encounters a problem, leading to unused cavities and reduced productivity.
- Clear or transparent plastic materials may not be suitable for gas assist injection molding as the cosmetic appearance can be negatively affected. By using pressurized gas to create hollow sections during the injection molding process known as "gas assist," clear plastics may lose their desired clarity and transparency. This is due to the appearance of flow lines or other surface flaws commonly referred to as "gas markings."
- The process requires specialized equipment and expertise, which can add complexity and cost to the manufacturing process.
- Some design constraints may arise due to the requirements of gas channeling and venting, limiting design freedom.
Is Gas Assist Injection Molding Expensive?
Yes. Gas assist injection molding can be more expensive compared to traditional injection molding processes. The equipment, tooling, and expertise required for gas assist can add to the upfront costs. However, the potential for material savings, improved productivity, and enhanced part quality can offset the initial investment. The overall cost-effectiveness depends on factors such as the specific application and production volume.
What Differentiates Gas Assist Injection Molding From Reaction Injection Molding?
As opposed to reaction injection molding (RIM), which combines liquid intermediates to form a polymer, gas assist injection molding (GAIM) involves injecting plastic and high-pressure gas to create hollow sections. GAIM makes use of thermoplastics and doesn't use polymerization, whereas RIM uses isocyanate and polyol that react to form a solid part. Both processes call for unique tooling and equipment.
Summary
This article presented gas assist injection molding, explained it, and discussed its process and purpose. To learn more about gas assist injection molding, contact a Xometry representative.
Xometry provides a wide range of manufacturing capabilities, including injection molding and other value-added services for all of your prototyping and production needs. Visit our website to learn more or to request a free, no-obligation quote.
Disclaimer
The content appearing on this webpage is for informational purposes only. Xometry makes no representation or warranty of any kind, be it expressed or implied, as to the accuracy, completeness, or validity of the information. Any performance parameters, geometric tolerances, specific design features, quality and types of materials, or processes should not be inferred to represent what will be delivered by third-party suppliers or manufacturers through Xometry’s network. Buyers seeking quotes for parts are responsible for defining the specific requirements for those parts. Please refer to our terms and conditions for more information.
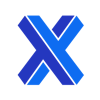